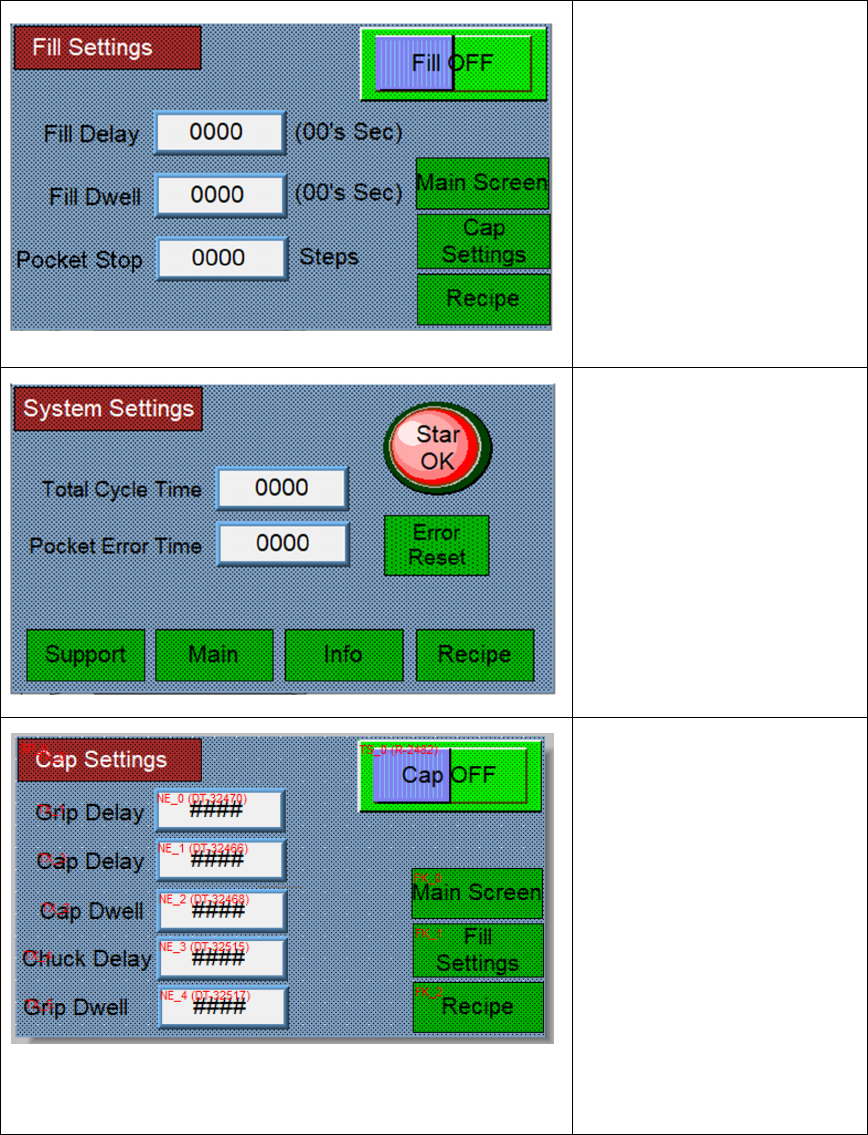
Filler Settings Screen
Fill On/Off: Push to Toggle On or
Off
Fill Delay: Push Number to enter
new delay. This is time for the
piston to dispense after the star
index is complete.
Fill dwell : Push Number to enter
the total length of the fill cycle.
This must be long enough to
allow the piston to fully stroke.
Pocket Stop: This is the number
of the star travel distance after
the index sensor triggers.
System Settings Screen:
Cycle Time: This is the total
length of the machine cycle, all
filling and capping functions must
be set within the length of this
cycle.
Pocket Error: If the star wheel
moves this many steps without
seeing a star pocket the machine
will stop and error( check that
the pocket eye and reflector are
working if this occurs)
Cap Settings:
Grip Delay: This number is the
time delay for the gripper to
extend to capture the bottle for
capping.
Capper Delay: This number is
time after the gripper closes
before the cap head lowers.
Capper Dwell: This is the length
of time the capping head stays
down for torqueing.
Chuck Delay and Grip Dwell:
These times are used with a
pneumatic chuck to delay the
closing of the jaws and delays the
opening of the gripper.